- Phillips Screwdriver
- Plastic Trim Tool Set (small flat-head screwdriver will also work)
- Scissors
- 3-M Super 77 Adhesive Spray
- Replacement foam, I used 1/4” High-Density automotive foam
- Staple gun (Optional)
You must be logged in to rate content!
10 minute read
HONDA ACCORD 2008-12 DOOR ARMREST INSTALLATION
Door Panel Removal Procedure
1. Remove the tweeter located in the door, to do this simply pull it in the direction indicated by the arrows with your hands, it should unclip and pop out. Then remove the single electrical connector from the tweeter and set this part aside. This step may be easier with the window rolled down.
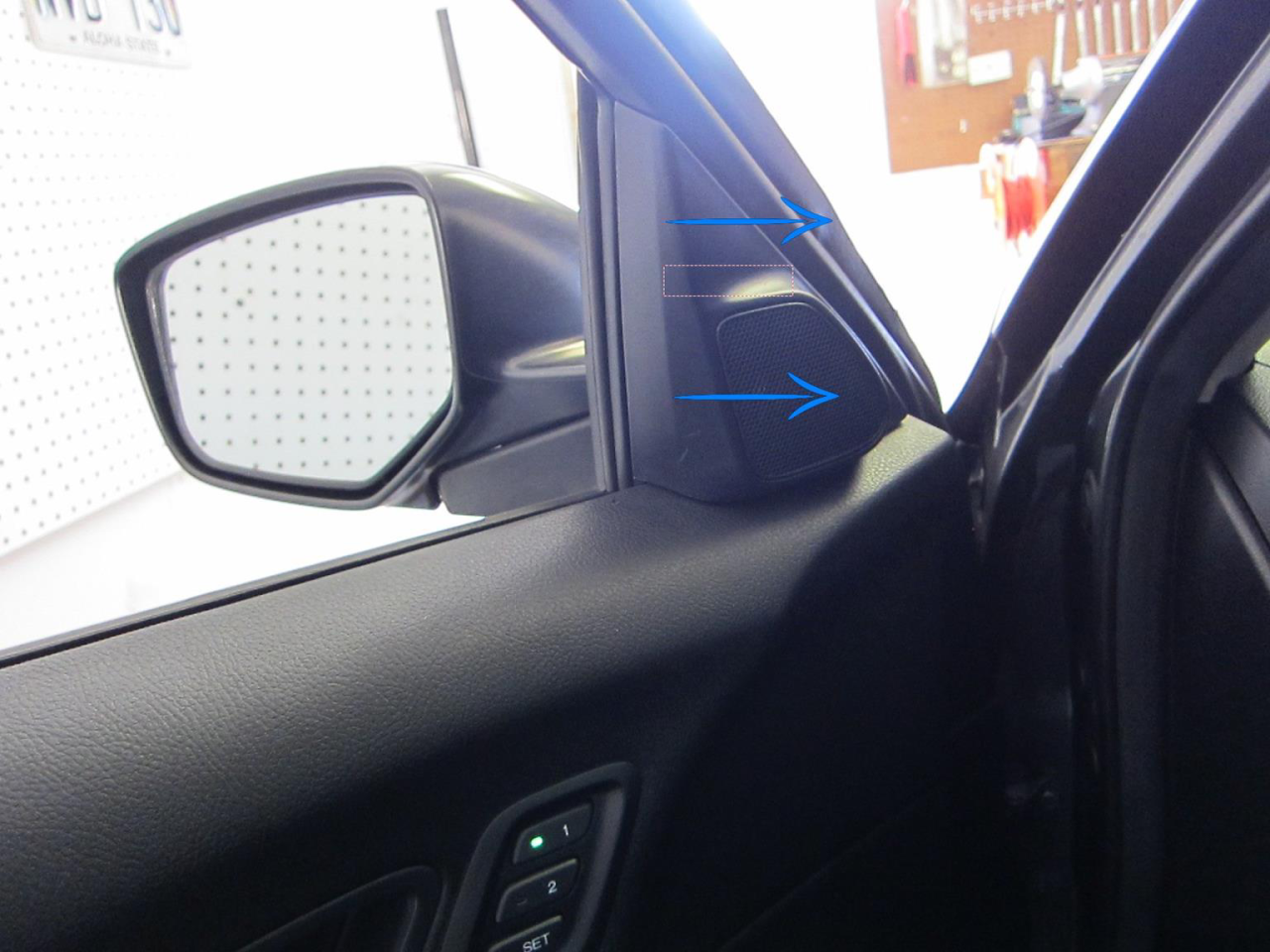
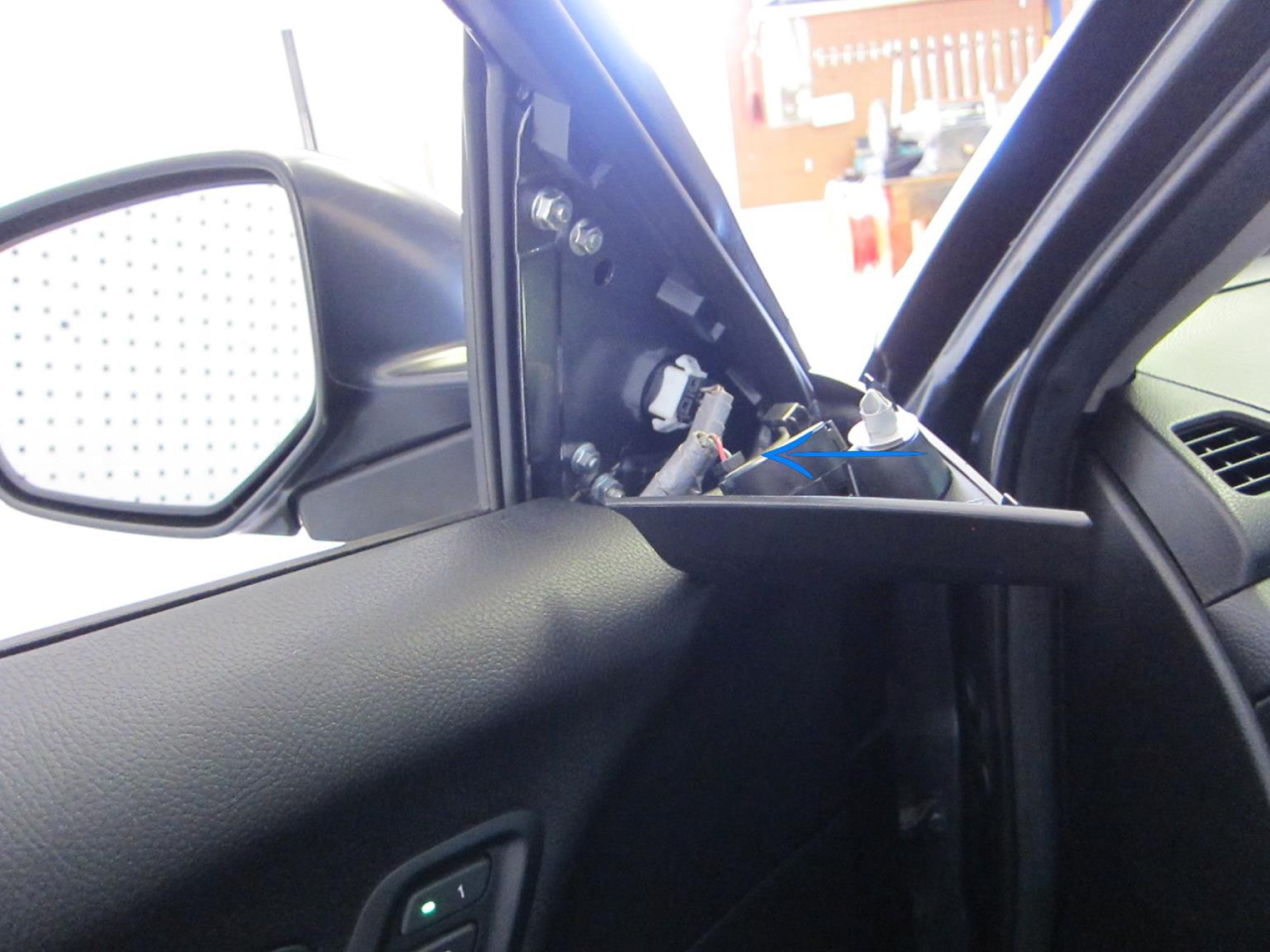
2. The next step is to remove the screws that are holding the door panel in, you will need your screwdriver and trim tool set for these steps. Use the trim tool set or small flat-head screwdriver to pop the panels off indicated by the arrows and use the phillips screwdriver to remove the screws indicated by the circles.
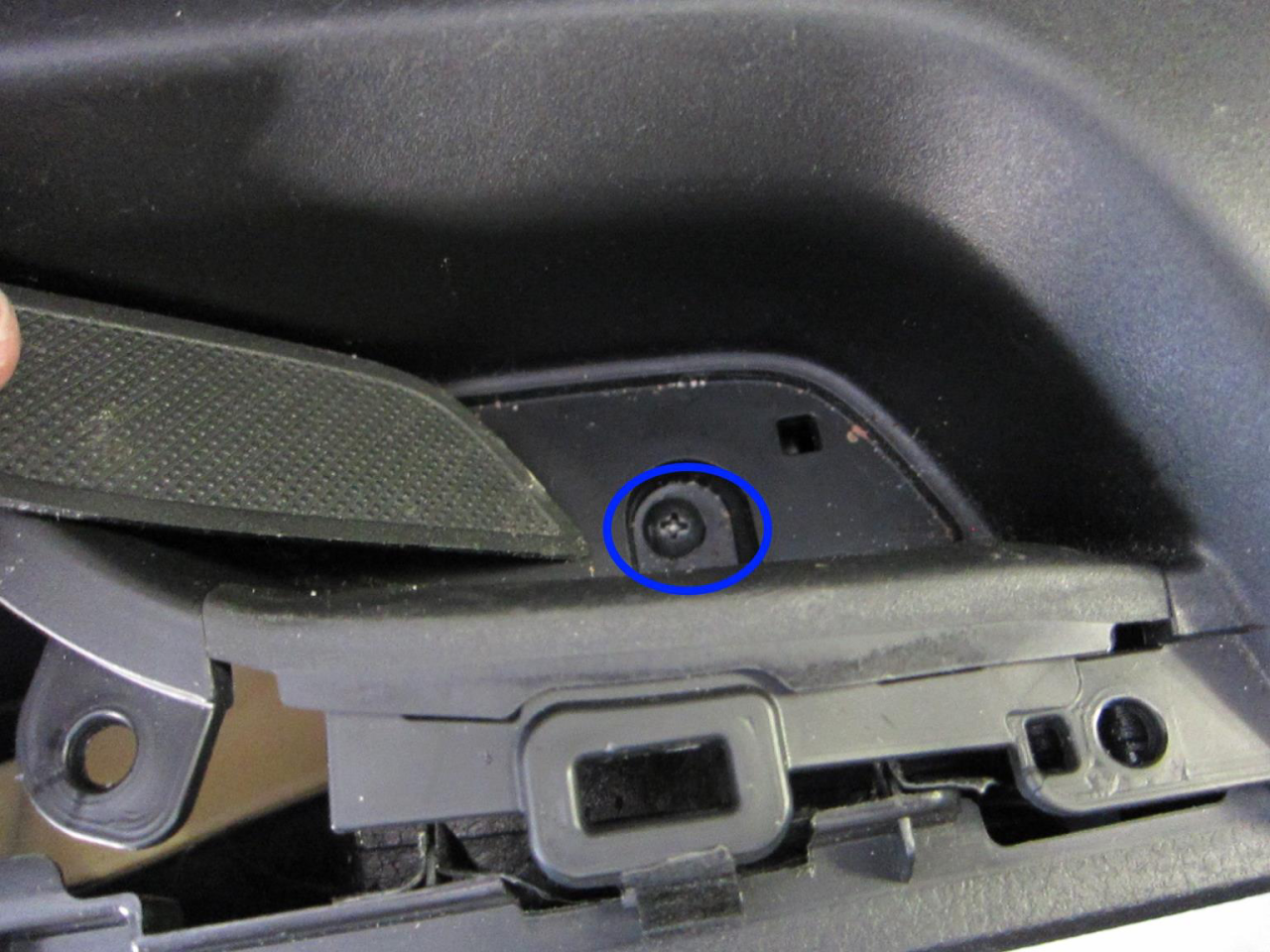
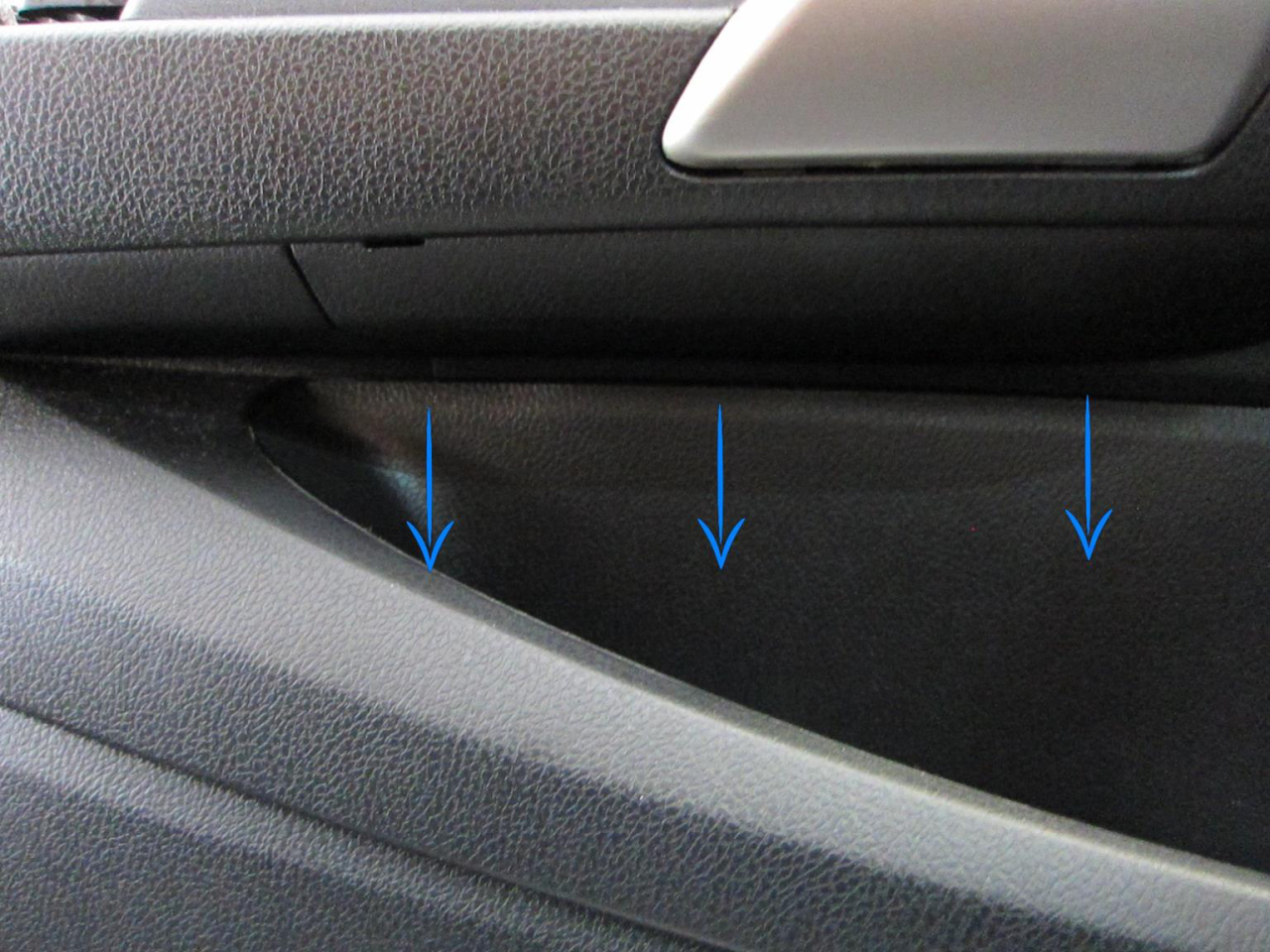
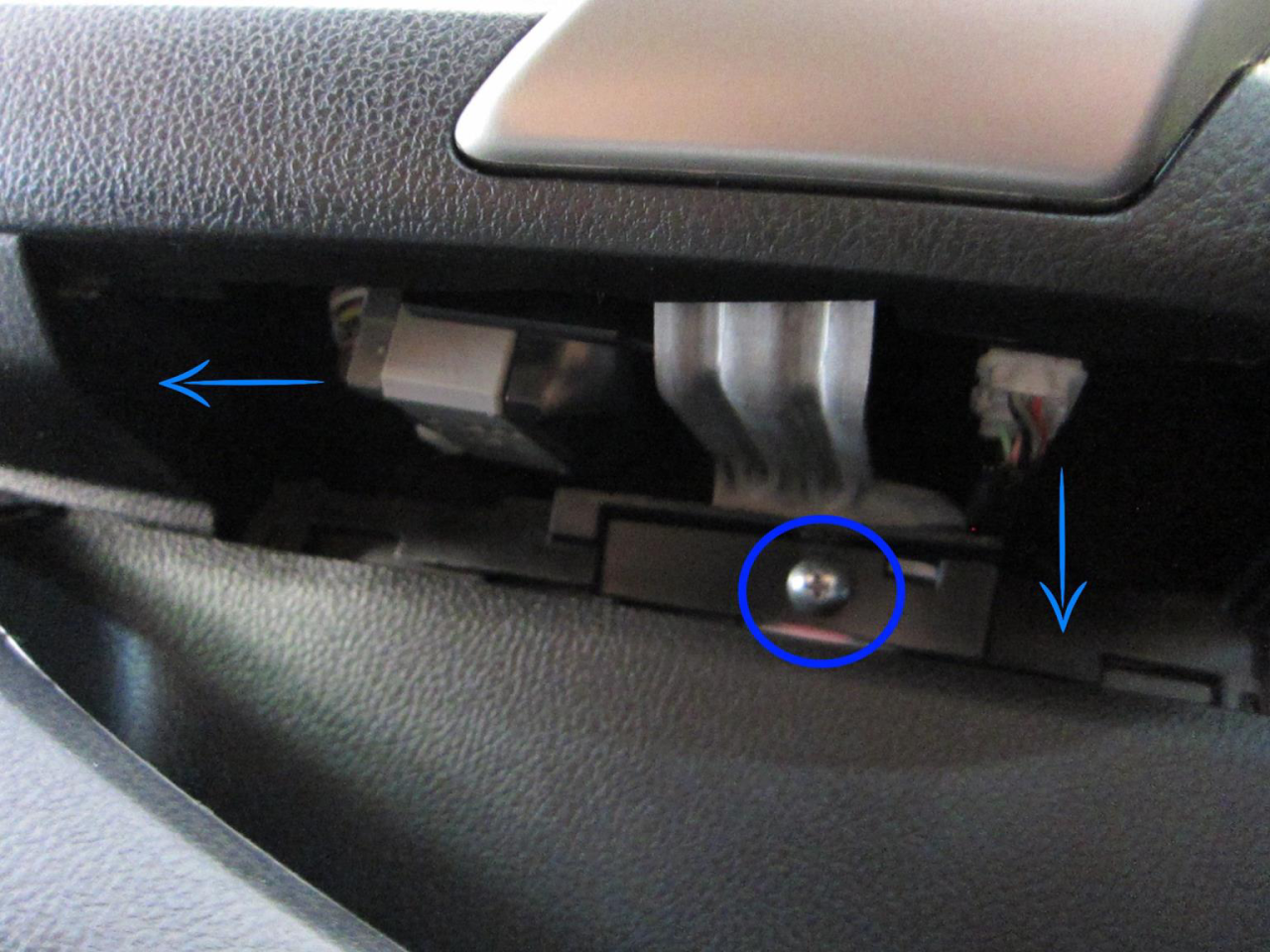
3. Disconnect the electrical connectors and screw indicated in the image above. The driver's side door is shown in the image, the passenger door is identical with one less electrical connector in this step. The connector on the left has a special clip and lever type of mechanism used to hold it in place present on both the driver's and passenger door. The clip must be pressed up and the lever pulled out in order for the connector on the left to be removed. All other electrical connectors have a single clip to depress and then pull out in the direction of the arrows. Be careful not to break any of the clips or pull any of the wires out of the connectors. For the clip type connectors they should be pulled straight out holding the connector. For the clip and lever type the action of moving the lever will remove the electrical connector from it's socket. A picture of the lever type connector is on the next page.
• For this connector the white clip inside the lever is depressed in the upward direction and then the lever can swing out. For re-installation simply place it in the socket and push the lever back in.
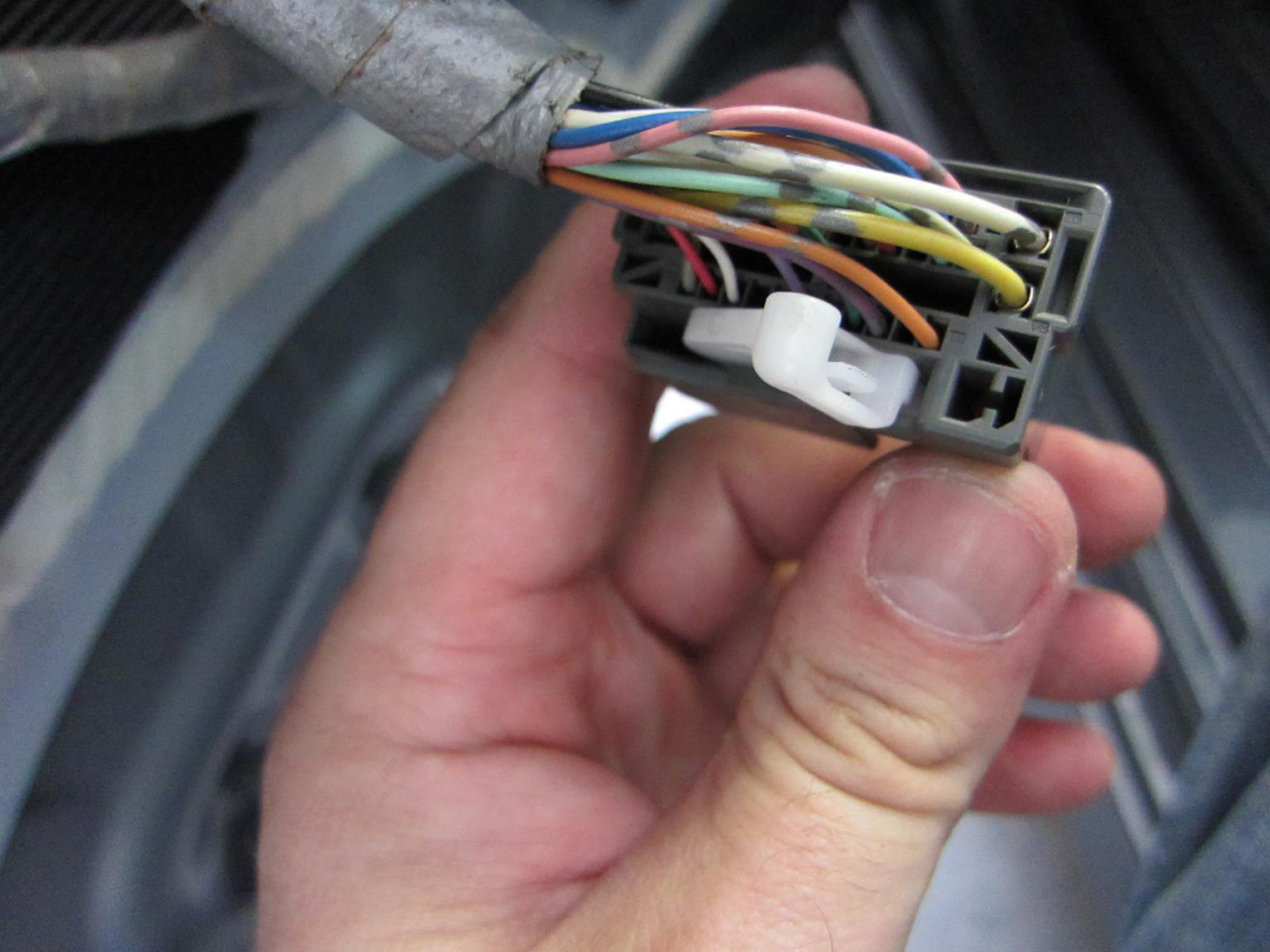
4. Next near the door lever remove the panel behind the lever by depressing the tab down with a small flat-head screwdriver or a trim tool and pull the plastic cover out.
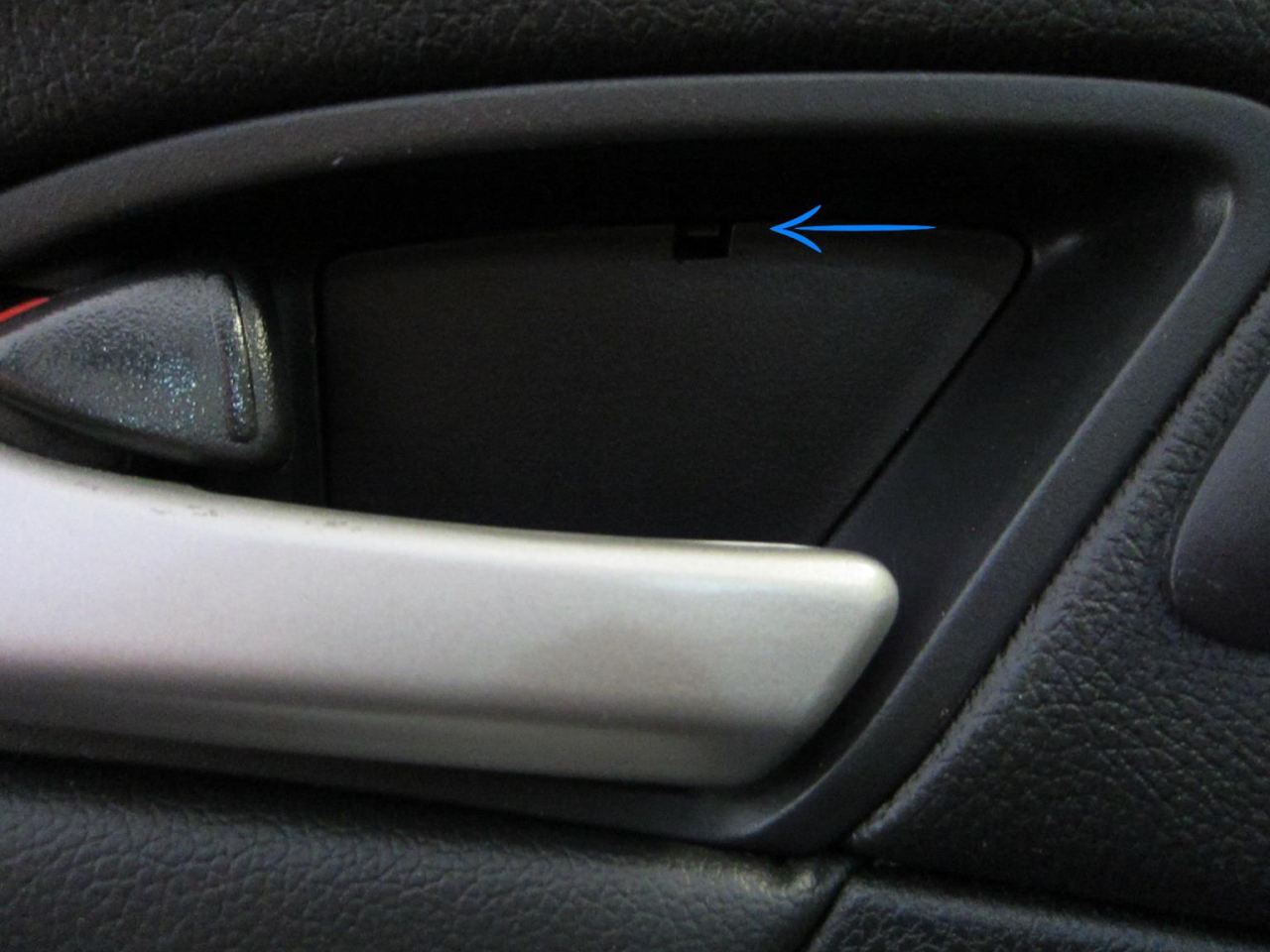
5. Remove three screws.
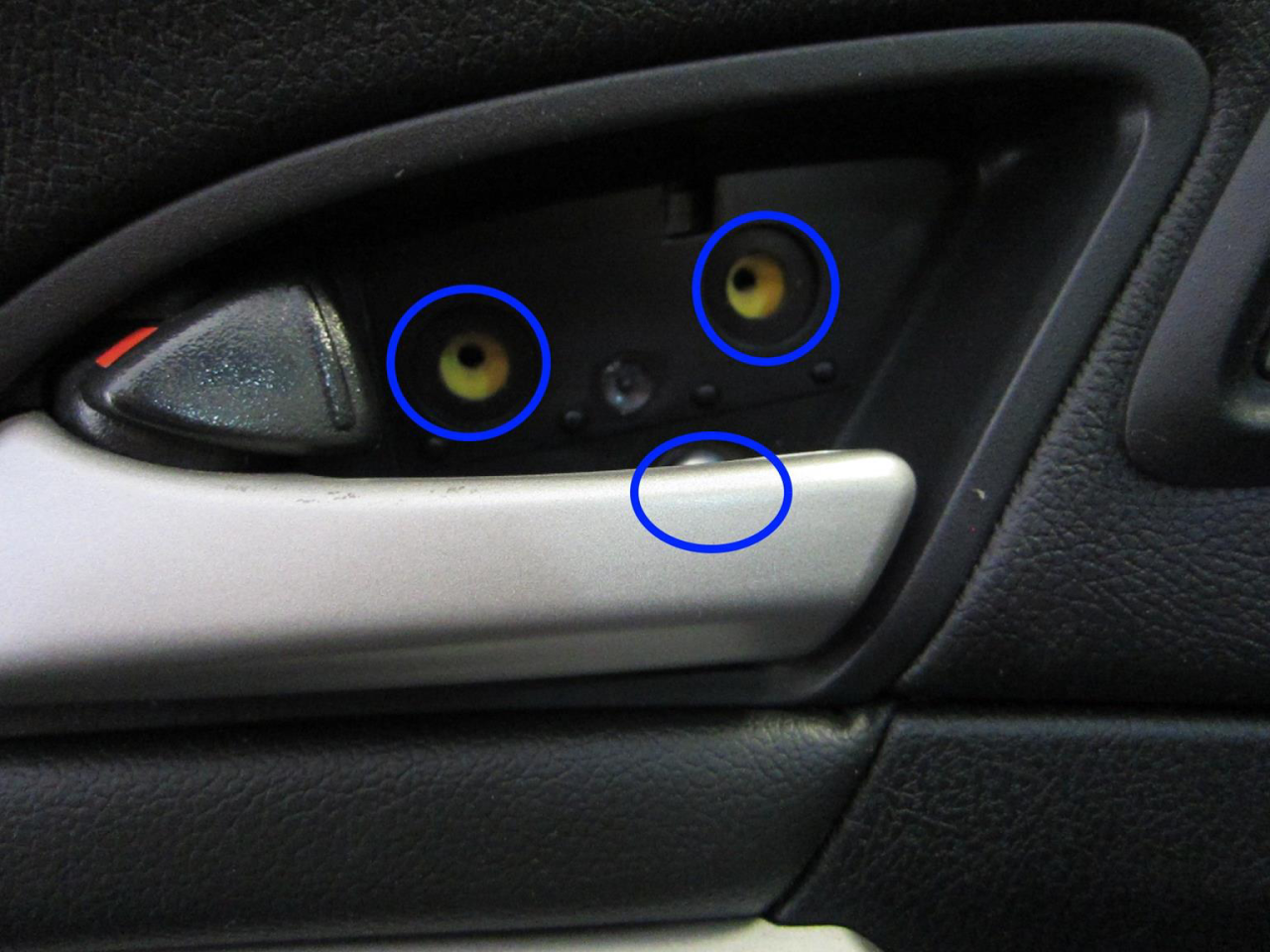
6. Next using a trim tool set or your hands pull the bottom of the door panel away from the door. It should unclip and pull away, being gentle as there is still an electrical connector inside the panel that must be removed if on the driver's door. The inside door handle can be pushed through the door panel at an angle and left connected to it's cable as it simply clicks into the door panel. Lift the panel up from the bottom once the bottom is free to free it from the top where it rests by the window seal it should look like the following image once away.
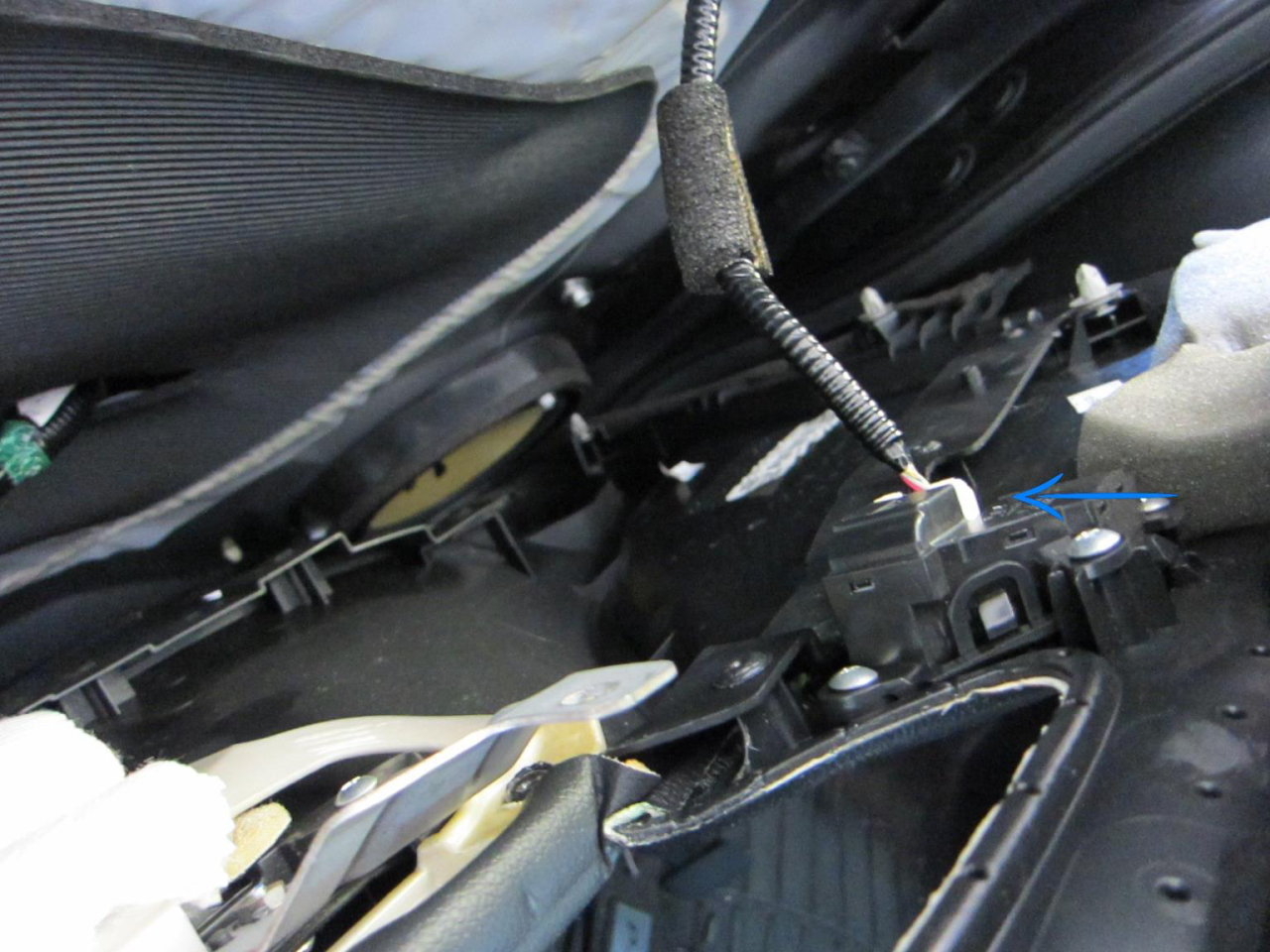
7. Next remove the single electrical connector and then pull the door panel away and place it on your work surface, it should be completely free from the door at this point, your door should look like the following image. This electrical connector is only present on the driver's side door.
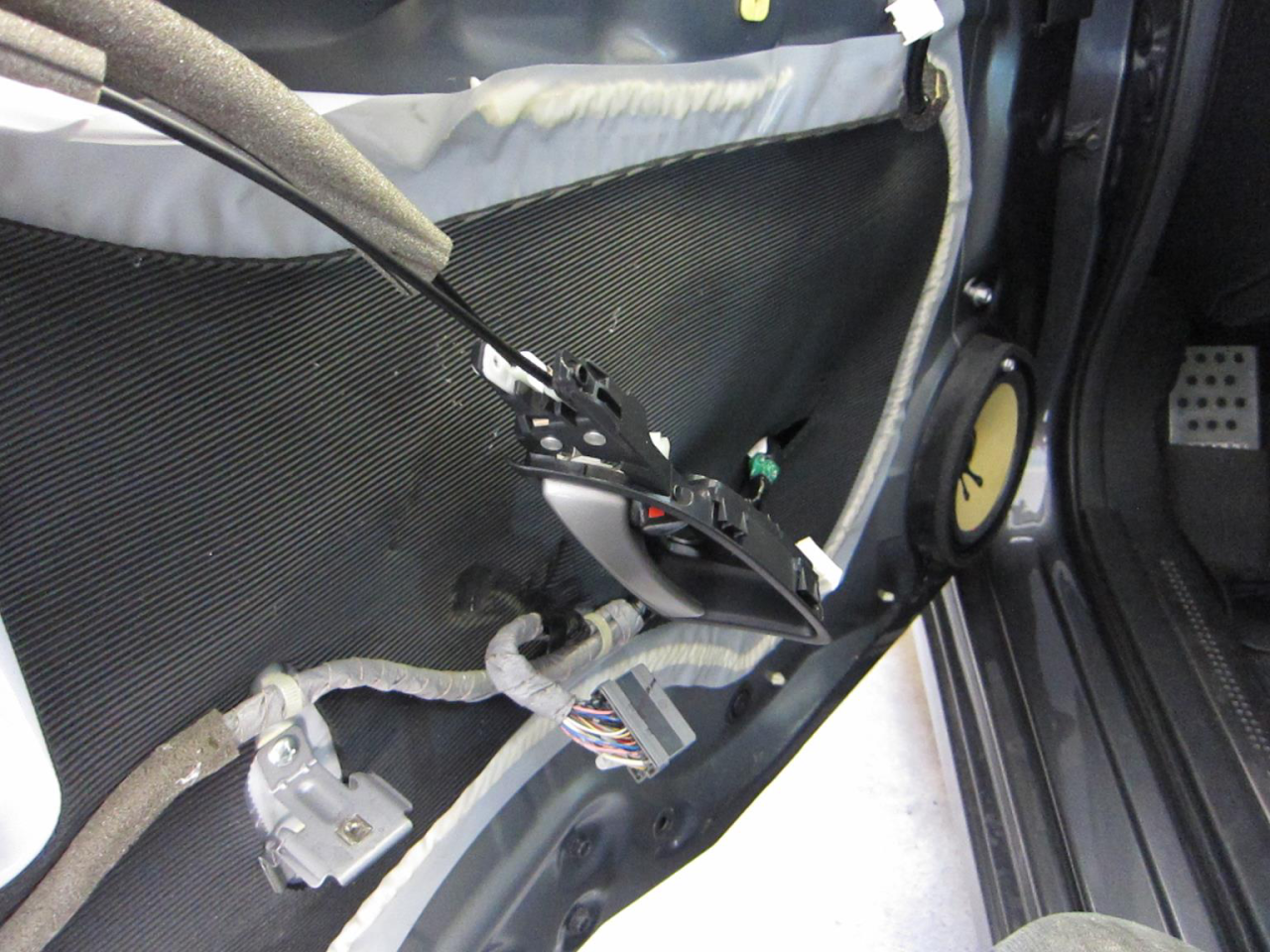
8. From here the door can be closed, no need to worry about the handle and it's cable, let it hang in place and move onto disassembly of the door panel.
9. The door panel does not need to be completely disassembled to remove the arm rest, instead just remove the screws circled and pop three clips on the
arm rest while pressing it gently away from the panel, there is one more screw on the opposing side to remove after these so do not try to completely remove the arm rest yet.
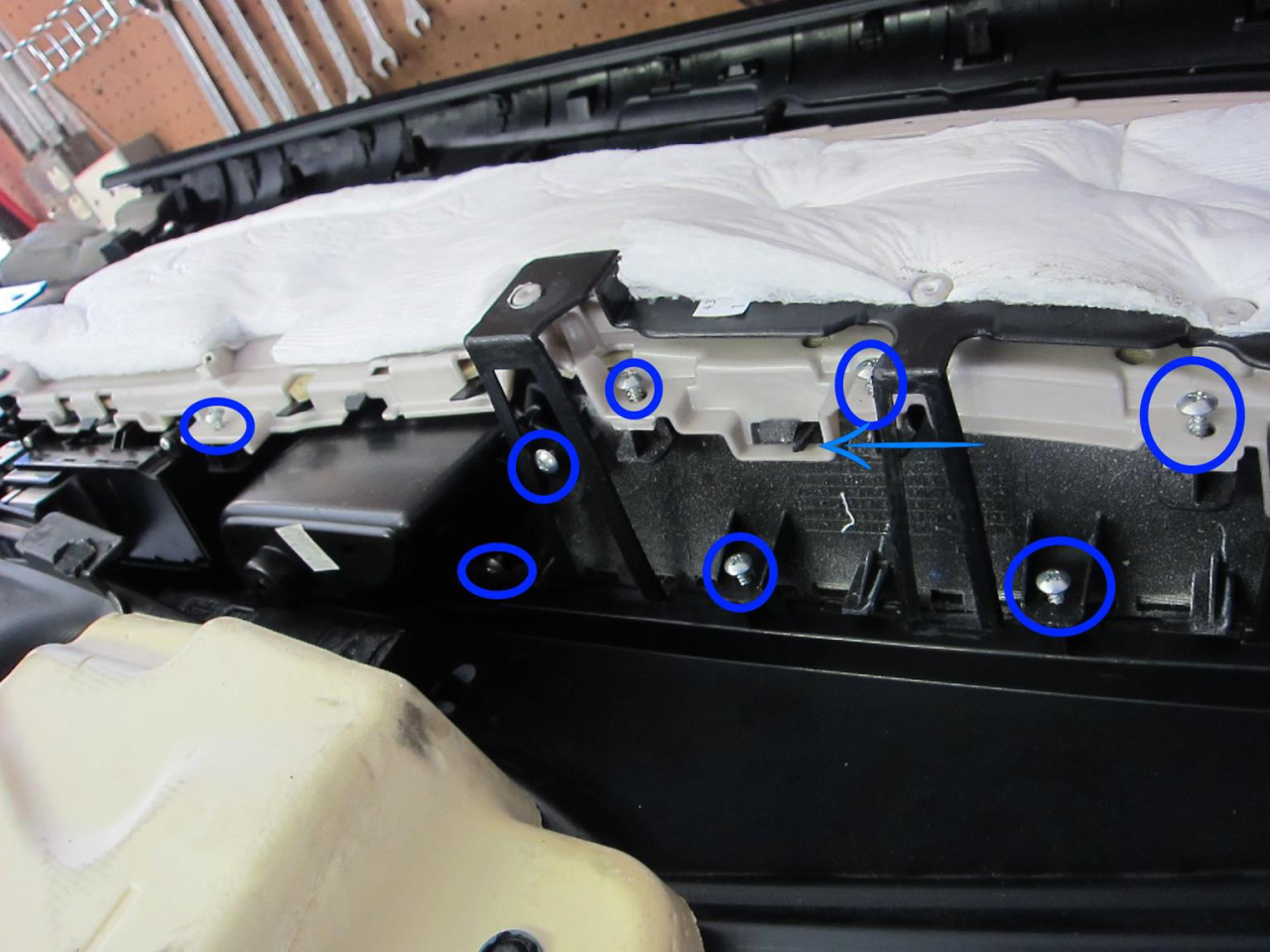
10. Here are is the last screw to remove before the arm rest will be liberated from the door panel. If you can not pull the panel up gently as shown it is because a clip or screw is still holding it in place on the other side.
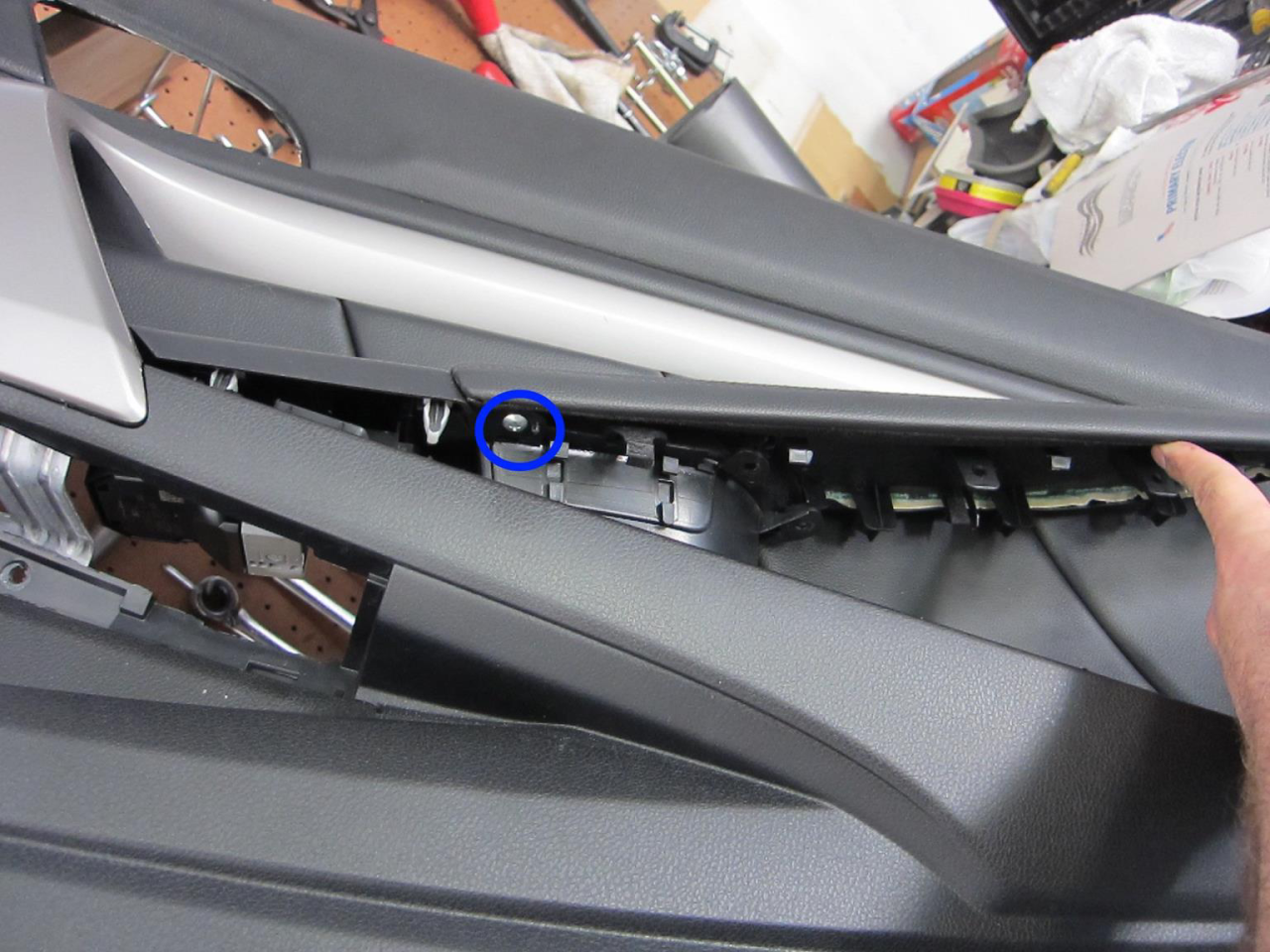
11. The next step is to remove the old fabric, simply peel away and remove all remaining foam that peeled away from the fabric. Do not remove the foam insert from the plastic arm rest panel.
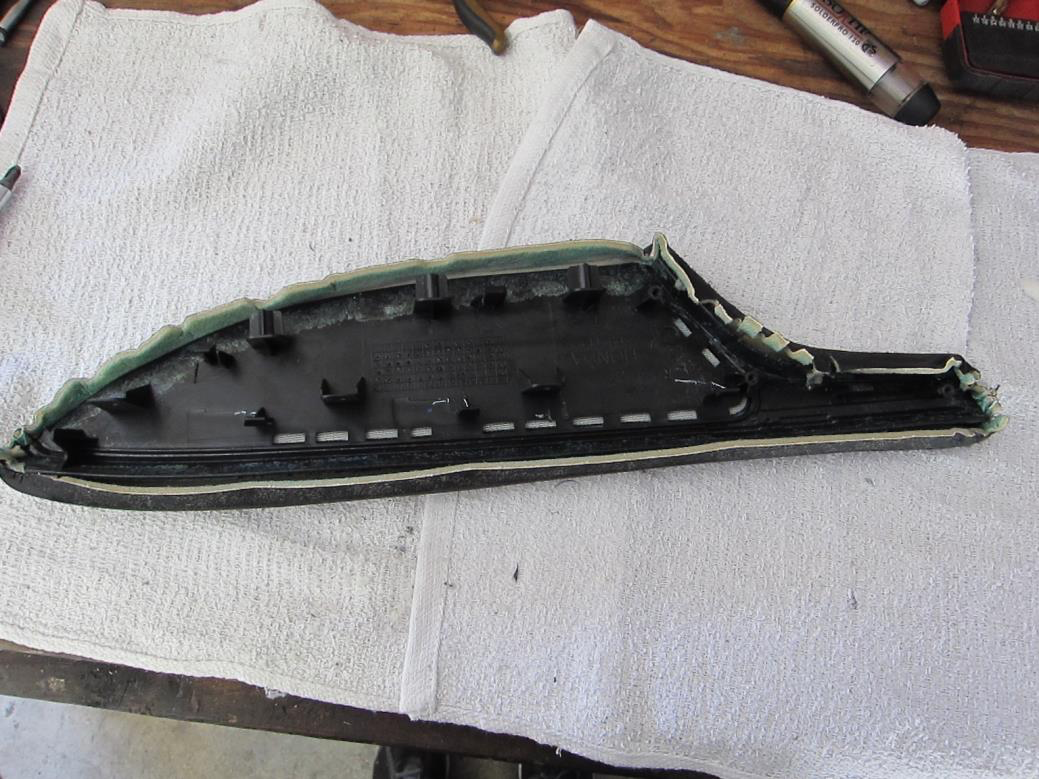
12. As you may notice most of the padding for the arm rest is sewn into the old
fabric, as such I am adding new foam.
I used 1/4” high- density
automotive foam and the fabric provided by Redline Goods was 'just' large enough to wrap over this new padding and the arm rest. I would, however, recommend having them extend the pattern about 1/8” all of the way around
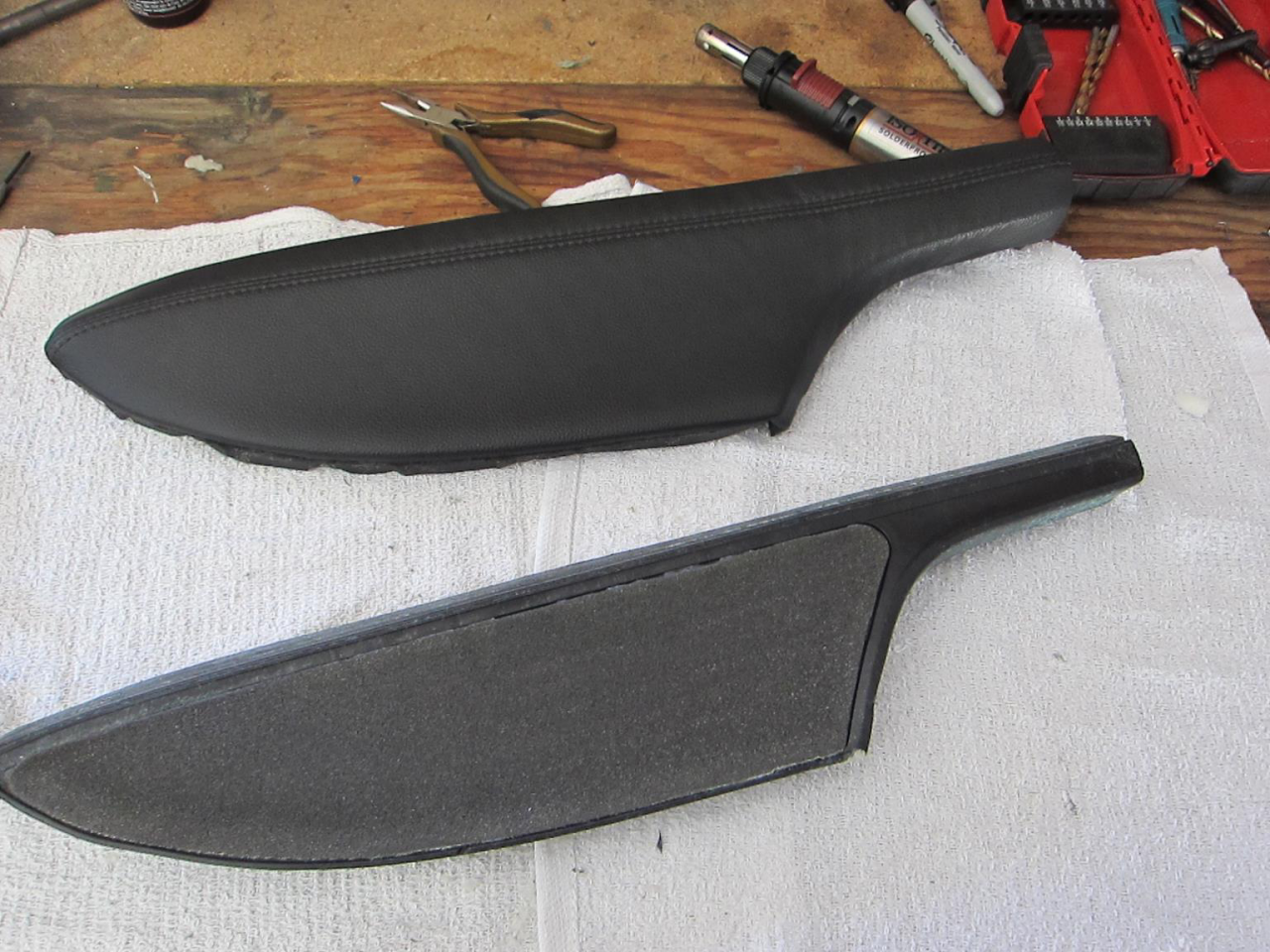
to make the wrapping job easier. The following images show how I used the new fabric to create a template in the foam and then cut it out.

13. The next step is to glue the foam to the arm rest, I utilize and would recommend 3-M Super 77 spray adhesive for this. Simply spray it on the arm rest and apply the foam, then trim it to the edges. Any unclean cuts in the foam from trimming will absolutely show through the fabric. It is very easy for an uneven or lumpy cut in your trim job to show through the fabric so the cleaner the cuts here the more professional the end product will look.
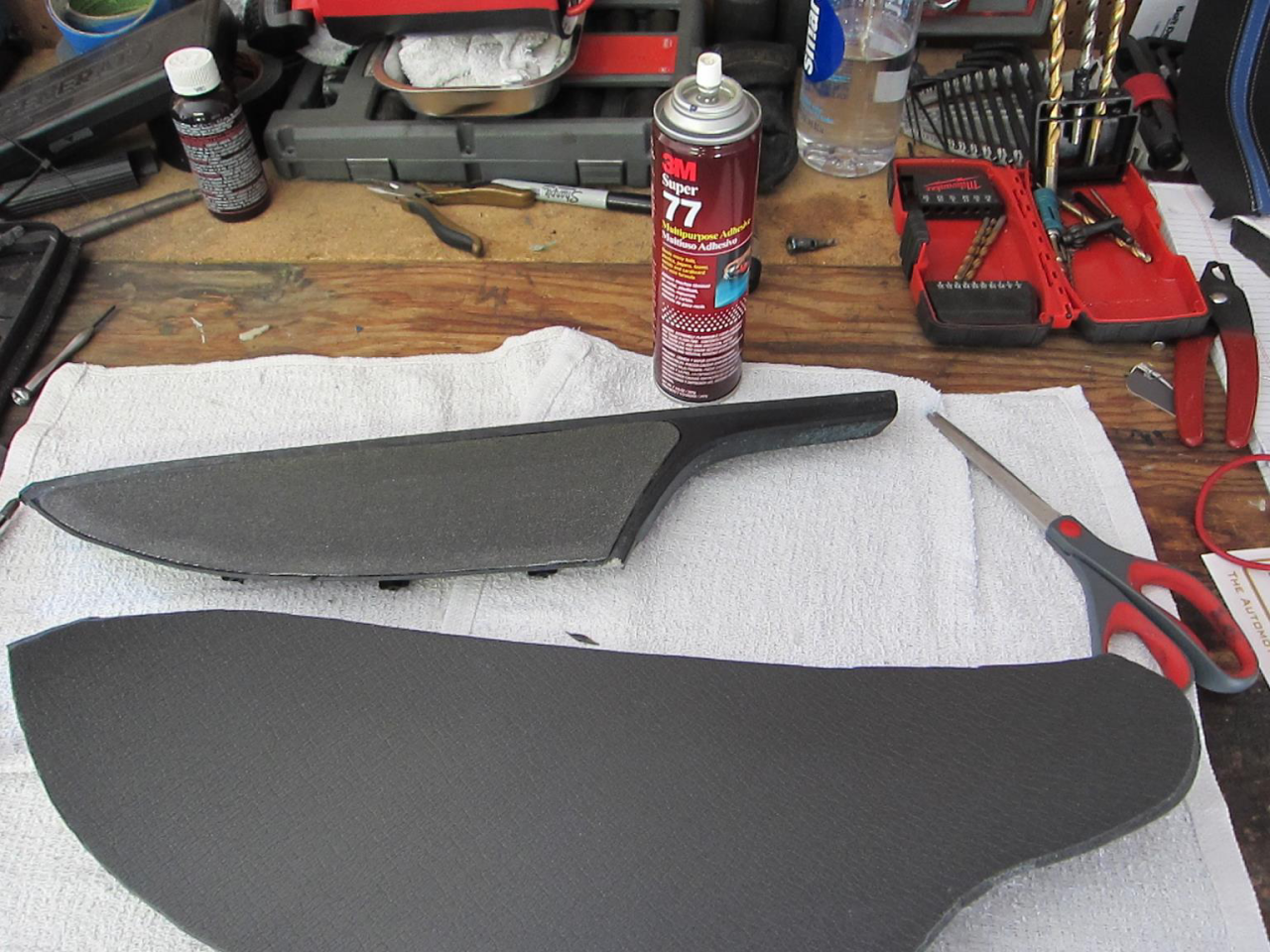
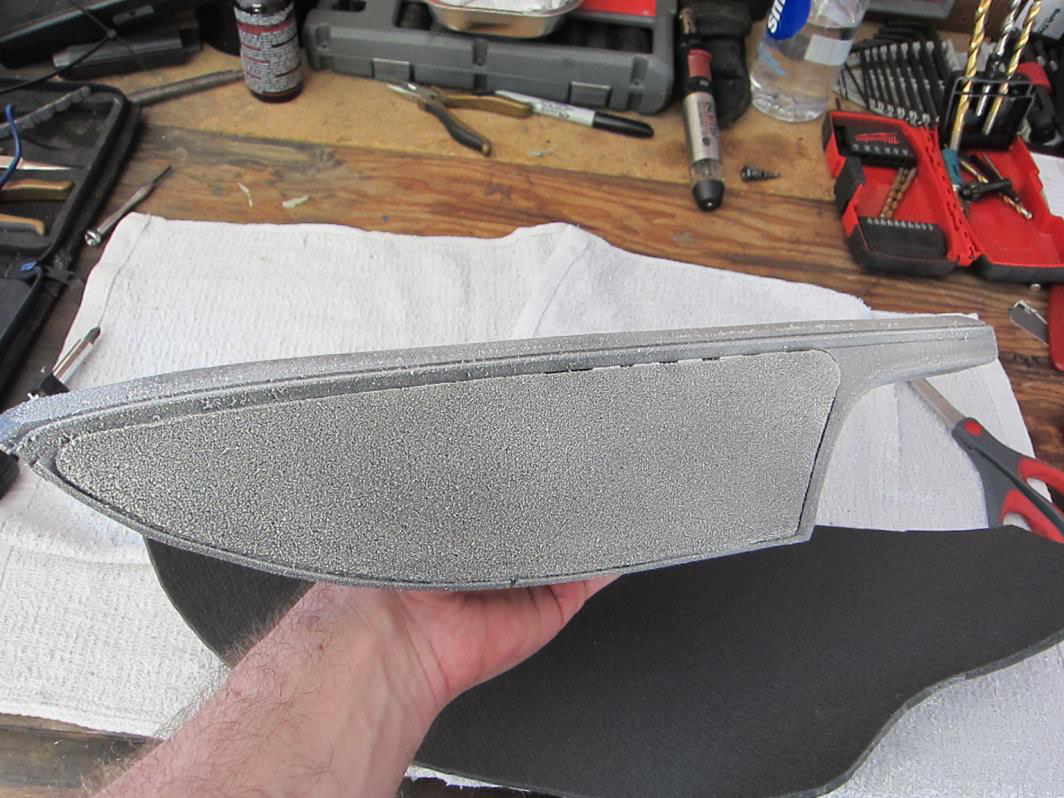
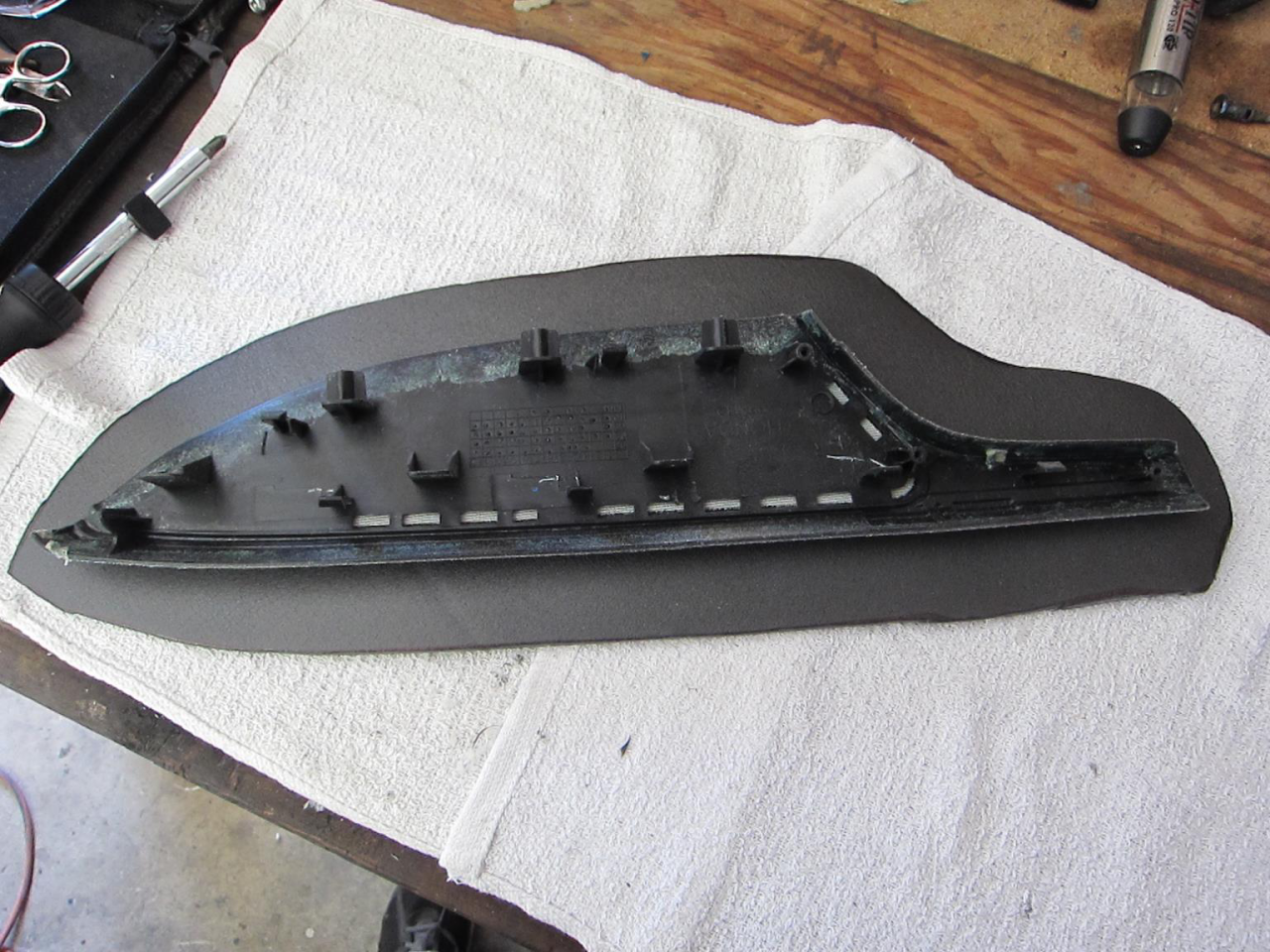
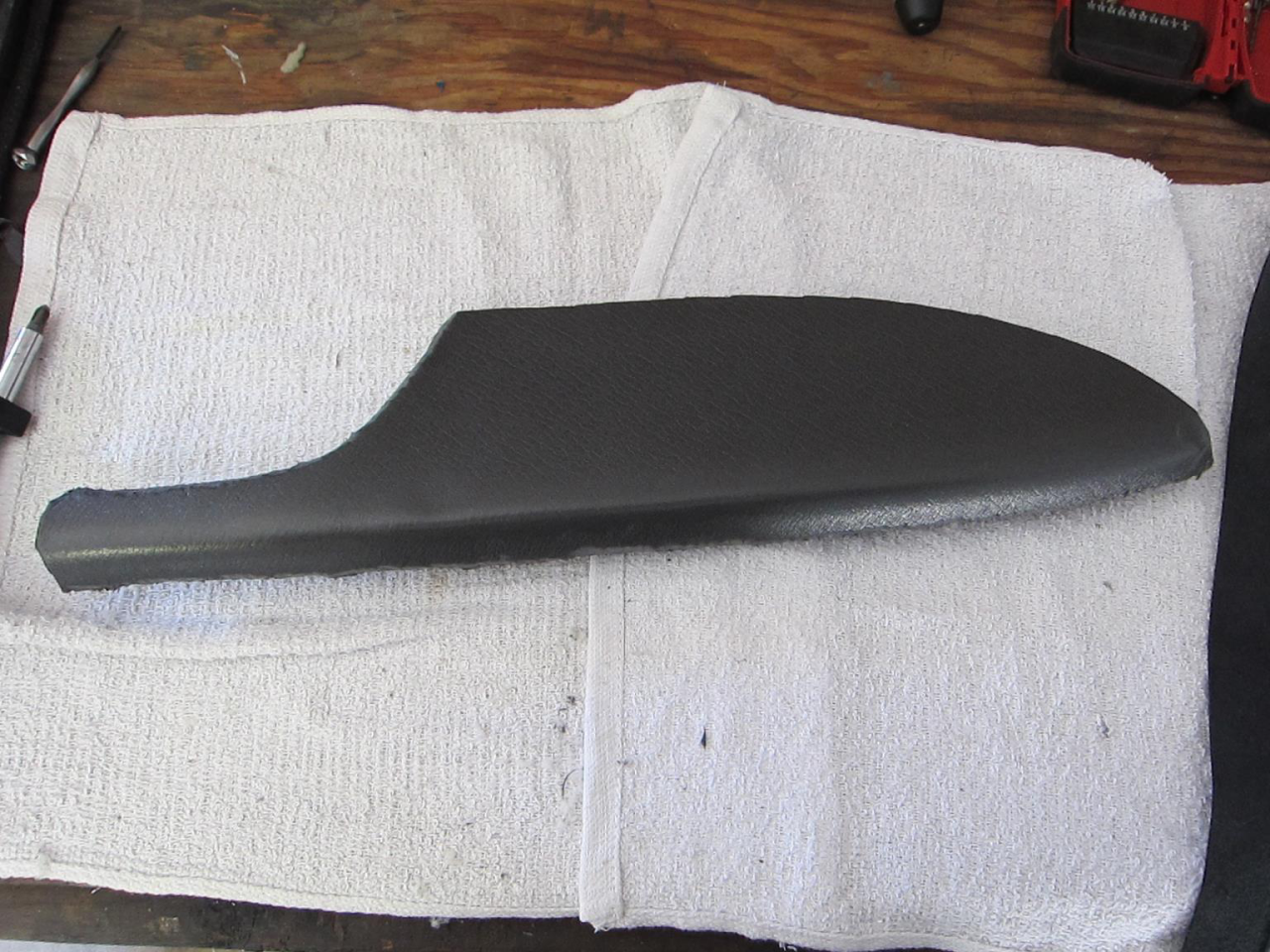
14. The next step will be to apply the fabric, before spraying any glue on the bottom of the arm rest cover I recommend laying the dry parts on your fabric, performing a test fit and marking the inside of the new leather with a felt-tip pen so you know where to lay it once there is glue on it prior to beginning your wrap of the part. When you are ready spray glue on the bottom side of the part. You can spray glue on the foam as well, however the leather will not be able to move during the wrap if you do so and that may cause problems during the wrapping of the leather. If you peel the leather away from foam that has glue on it the foam will rip and stick to the leather and if all of this ripped foam is not removed, made completely even again on the inside of the leather and replaced on the plastic arm rest prior to assembly any unevenness of the foam will show through on the final product very easily.

15. As you can see from this picture with the 1/4” high density foam that I chose to use there is barely enough leather to wrap the tips on the part. You also may need to increase the length of the cuts at the curve in order to get a smooth fit during your wrap procedure (you likely will). Just be sure not to cut too far or you will see the cuts in the finished product once everything is re-assembled. Staples from a staple gun may also help, but will likely not penetrate very far into the plastic unless you have some type of pneumatic staple gun. I use the hand-held type and it does help but staples do not penetrate all of the way into the plastic and many of them may not penetrate at all or will fall out easily. This is the most important step for a professional looking job.
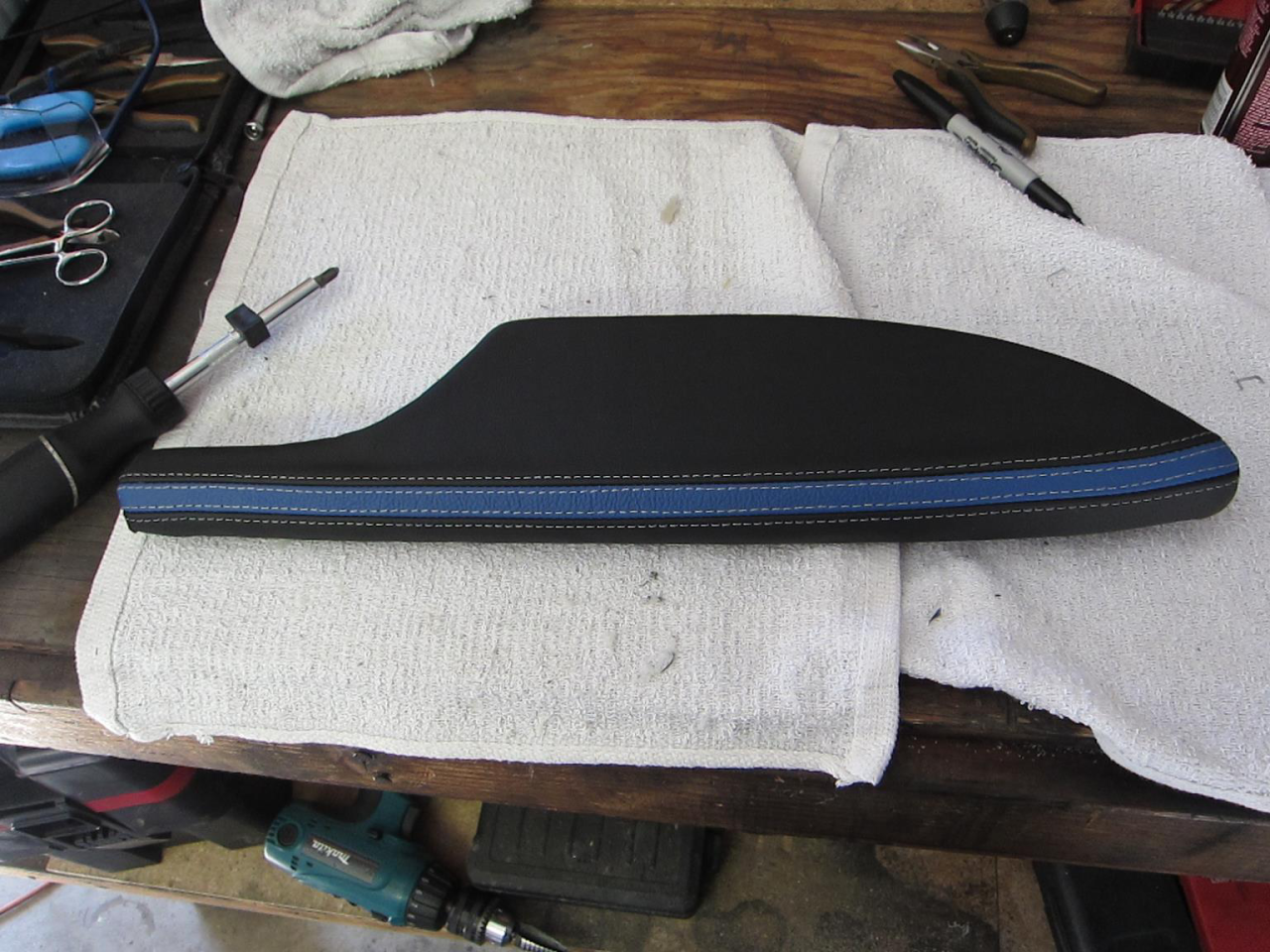
16. Once done you're good to go, re-assembly is the reverse of the removal process. Some of the screws and clips will help hold the leather in place, particularly the very last one that was removed in the disassembly process. Make this one tight and tuck the leather in with a small flat-head screwdriver or trim tool carefully for a professional look. The following page has a few pictures of my car, I've gone with Redline's nappa leather with medium blue leather stripes on the front-back axis and silver stitching.
17. Enjoy!
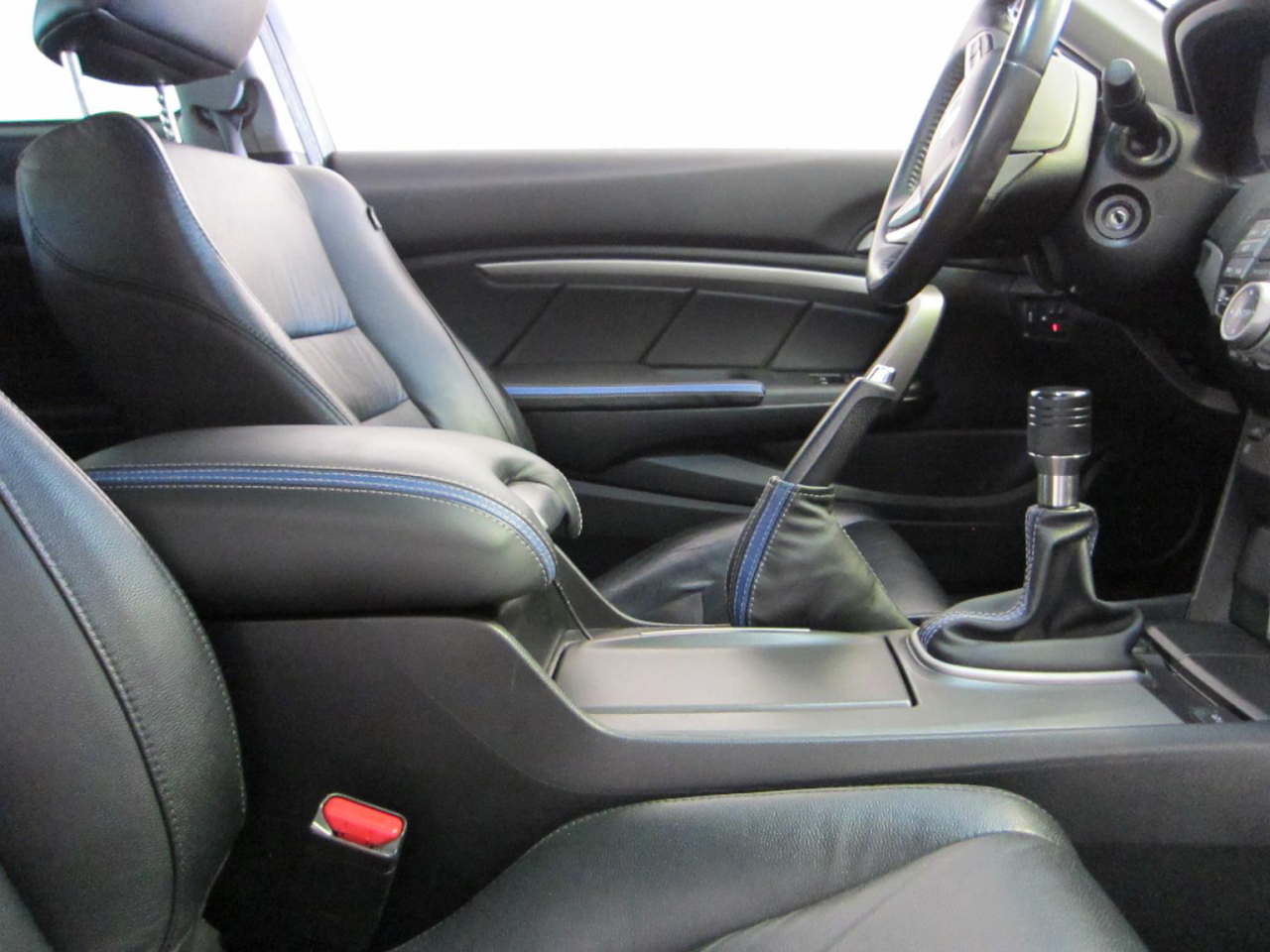
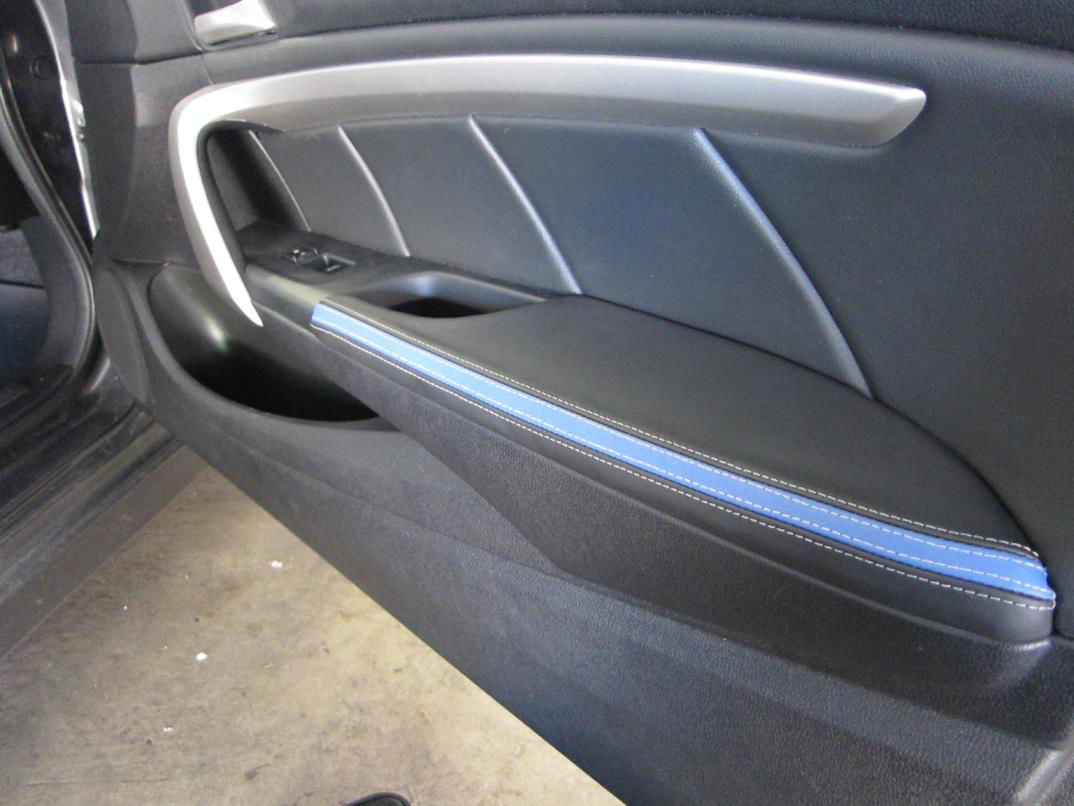